Because every single component is designed to be disassembled and reused, no waste is produced at any stage of a building’s lifecycle.
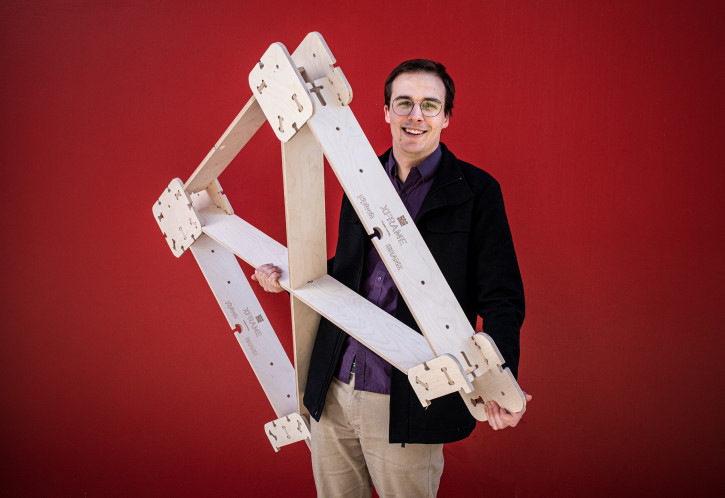
Approximately half of all New Zealand's waste—about 1.6 million tonnes every year—is generated by the construction sector.
The current widespread use of adhesive-based fixings and single-life materials means that building a single new home will create about four tonnes of waste during construction, and even more when it’s eventually demolished and taken to the landfill.
A Victoria University of Wellington architecture student—Ged Finch—is working with Wellington UniVentures to commercialise a game-changing building design that has the potential to eliminate waste and reduce the amount of raw materials being used by the building industry.
His idea centres around a framing system that can be disassembled and re-used at the end of a building’s useful life—an architectural solution he hopes will transition the building sector from a linear (take, make, dispose) economy to a circular economy—where materials are reused in endless cycles.
Features and benefits
Zero waste
Easy to assemble
The self-braced, interlocking design enables pieces of wood to simply clip together like flat-pack furniture, enabling rapid assembly/disassembly using unskilled labour and a bare minimum of tools.
Easy to customise
The clip-together design means that any type of structure—floors, walls, ceilings—can be created, while adding doors or windows - and even additional rooms - is made simple.
Wellington Gold Awards 2021
WGA Text
The Wellington Gold Awards honour the region’s business talent and pays tribute to those who are building the Wellington community. X-Frame was named as a finalists in the Innovation Gold category.
Watch their entry video here.
Next steps
After Wellington UniVentures introduced Ged to KiwiNet in 2019, the young entrepreneur was accepted into the KiwiNet Emerging Innovator Programme; he is now using the funding and mentoring he's received from the programme to finalise engineering designs for the earthquake-resistant, hold-down fixings for the walls and interior. Ged is also testing the structural integrity and weather-tightness of the X-frame product—with financial assistance from BRANZ as part of his PhD scholarship with the independent research organisation.
Once testing is complete, Ged will undertake a series of small-build prototypes in the form of a cabin and a sleep-out to demonstrate his ideas at scale—all while taking part in a nine-month Circular Economy Programme with an Australian-based incubator, and working with Wellington UniVentures to establish the best pathway to market. One option that he is currently exploring involves using X-Frame in the commercial interior fit-out market.
We are now seeking industry partners to help commercialise this technology. Get in touch with the Commercialisation Manager below to find out more.
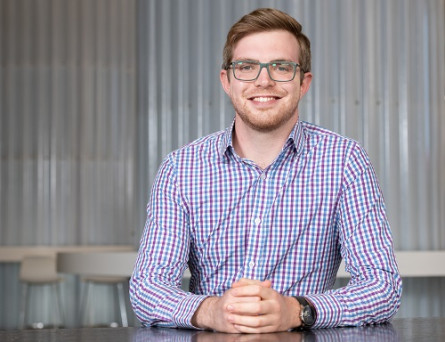